Linde automatise sa production de chariots
À l’occasion du lancement de sa nouvelle génération de chariots frontaux électriques, le fabricant Linde Material Handling, dont les produits sont commercialisés en France sous la marque Fenwick, a ouvert les portes de son site d’Aschaffenburg, à 40 km de Francfort. L’occasion de découvrir une production automatisée.
____________________
Par Christophe Duprez
Publié le 2025-05-28
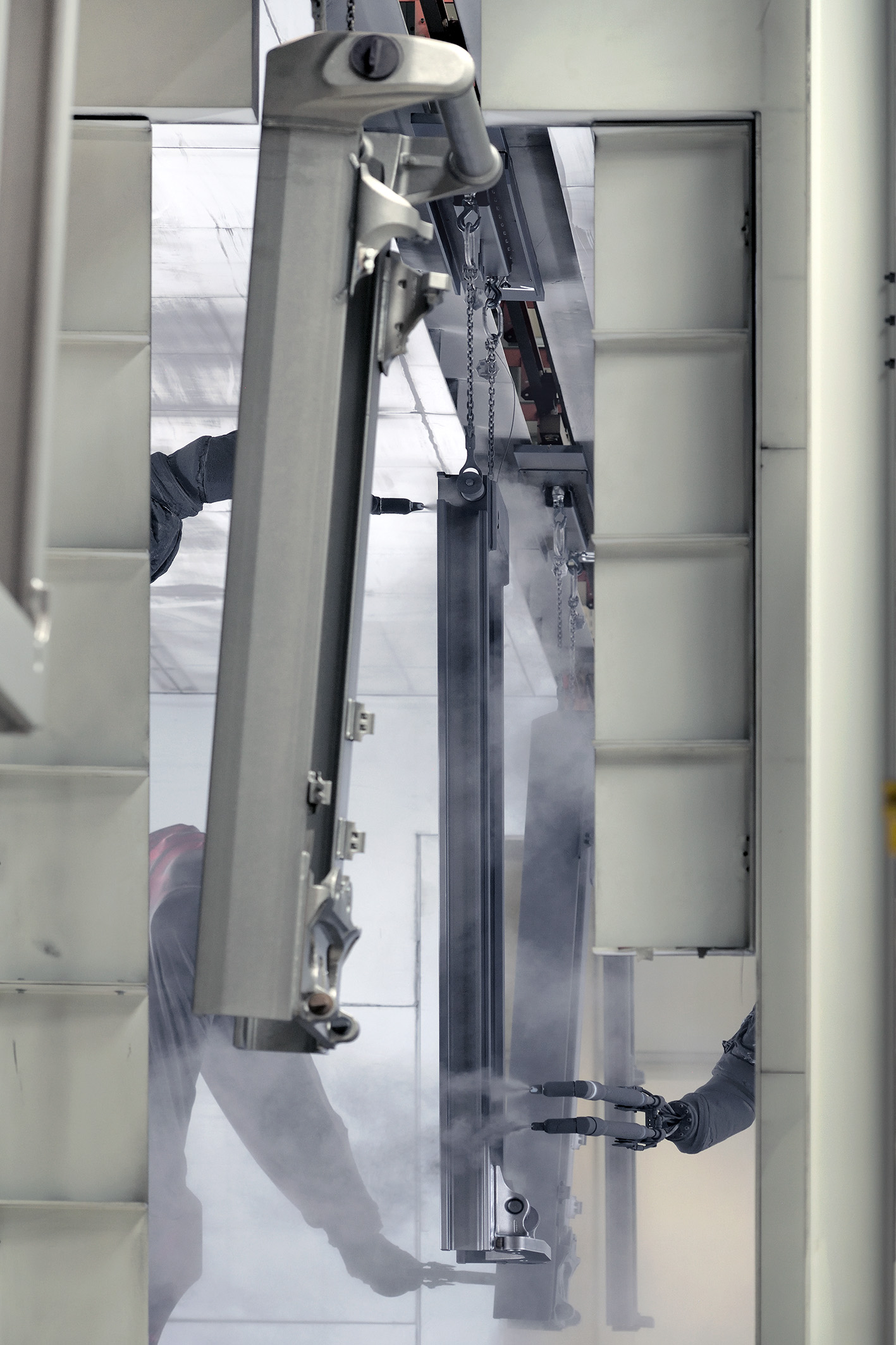
Siège social et usine se côtoient. Ici, à Aschaffenburg, en Bavière, se trouve le plus grand site industriel du groupe Linde Material Handling. Les 15 halls qui le composent s’étalent sur 300 000 m2, chacun ayant des fonctions bien spécifiques. Quelque 2 200 collaborateurs, répartis à parts égales entre la production et l’administration, mettent sur le marché 45 000 chariots par an.
Tout débute dans le bâtiment dédié à la R&D où sont conçus et développés les chariots frontaux thermiques et électriques, d’une capacité de charge de 1 à 8 t. « Les nouveaux modèles de 1 à 2 t que nous lançons aujourd’hui représentent le fruit de six années de travail », précise Anthony Vernizeau, responsable marketing Produits & Énergies au sein de Fenwick-Linde(1), la filiale française de Linde Material Handling.
L’assemblage des chariots ne démarre qu’une fois la commande finalisée. Dans un premier temps, l’usine est approvisionnée par une fonderie du groupe, située à une vingtaine de kilomètres, qui fournit la plupart des pièces et des éléments mécaniques : mâts, contrepoids, cabines…
Une fois soudés dans le hall 1, les mâts, éléments centraux du chariot, sont recouverts d’une
peinture en poudre sèche appliquée par des robots dans le hall 2. Les quelque 120 000 montants qui les constituent voient ainsi le jour chaque année et sont assemblés en fonction des besoins des clients. Il est donc rare que deux mâts soient semblables.
LE CŒUR DE L’USINE
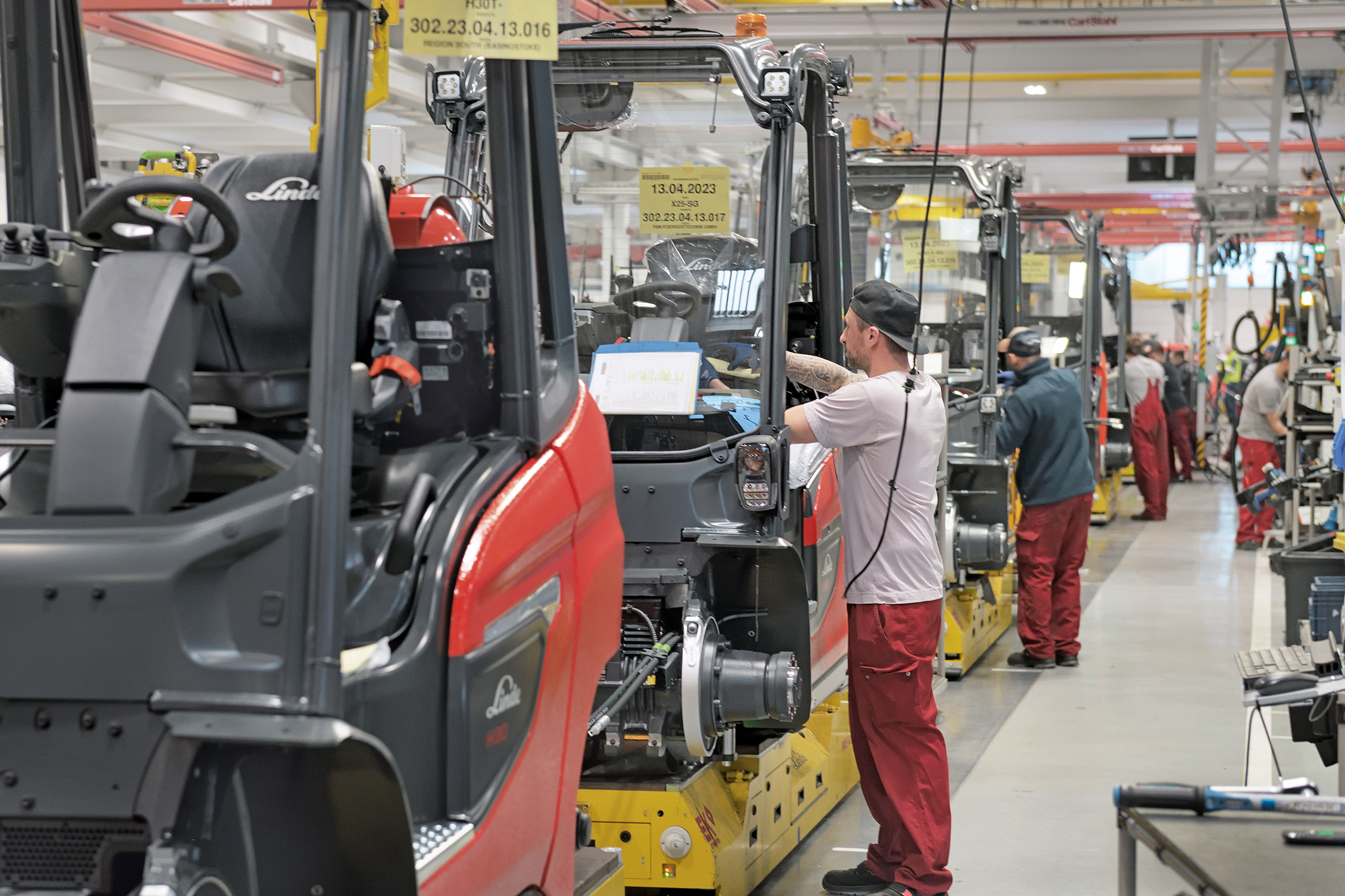
Mais, pour René Wichmann, directeur senior du site, « c’est le hall 4 qui constitue le cœur de l’usine ». Là se trouvent, en effet, les trois
lignes d’assemblage accueillant des chariots de tailles et de motorisations variées. La première couvre les modèles de 1 à 3,5 t, la deuxième de 3,5 à 5 t, et la dernière de 5 à 8 t. Sur le châssis sont successivement montés le contrepoids, la motorisation, les essieux puis la cabine, avec ses différents éléments. Châssis et cabine sont ensuite soudés et peints. Les mâts sont ajoutés en dernier.
Si certaines de ces parties, comme les parebrises, ne sont pas produites en interne et proviennent de multiples fournisseurs, le constructeur assure que ceux-ci sont très majoritairement européens.
Toutes ces opérations de montage, opérées en deux-huit et à flux tendu, font l’objet de séquences d’une douzaine de minutes. « La production ressemble beaucoup à celle que l’on trouve dans l’automobile, remarque Anthony Vernizeau. Nous avons automatisé notre chaîne autour du châssis qui est amené sur AGV [véhicules à guidage automatique] ». L’ensemble du processus étant numérisé, la qualité du montage, et en particulier du vissage, est vérifiée en temps réel par des outils d’assemblage à chaque poste de travail. Évidemment, un opérateur intervient sur des modèles de chariots souvent différents.
Une fois l’engin terminé, il est soumis à une batterie de tests puis stocké, le temps de compléter le chargement d’autres modèles.
Un nouvel entrepôt logistique automatisé sera prochainement doté d’une passerelle aérienne de 400 m de long. Il est destiné à limiter les flux par transport routier. La nouvelle infrastructure procurera plus de confort aux salariés et réduira l’empreinte carbone globale. En effet, cet entrepôt remplacera cinq lieux de stockage situés à plusieurs kilomètres, à la source d’un manège quotidien de plus de 200 camions. Les chariots siglés « Fenwick » sont in fine envoyés à Marly (Nord), où ils peuvent, si nécessaire, être adaptés aux besoins des clients français.
DES CHARIOTS CONNECTÉS
Mais le potentiel technique de ces nouveaux chariots frontaux électriques ne s’arrête pas là. Chaque engin est en effet doté de capteurs destinés à collecter des informations sur son utilisation, par exemple la fixation ou non de la ceinture de sécurité par le conducteur ou encore le nombre d’heures de roulage.
Ces informations sont ensuite communiquées, via Bluetooth, wi-fi ou GPRS, à un logiciel de gestion de flotte, dans un serveur, où chaque machine se voit associée à un dossier numérique. En analysant les données ainsi récupérées, les clients sont en mesure de mieux comprendre l’usage qu’ils font de leurs chariots. De son côté, Linde, pour qui ces données sont également accessibles, peut mettre à jour à distance les logiciels des engins, activer certaines fonctions sans l’intervention d’un technicien ou anticiper une maintenance.
« Chaque client ayant un niveau de connaissance variable, nous sommes en mesure de développer des solutions correspondant aux spécificités et connaissances de chacun », souligne Jan-Niklas Freund, responsable du département Automatisation.
La connectivité des chariots devrait donc être profitable à la fois aux clients (meilleur retour sur investissement), aux caristes (meilleure ergonomie) et, bien sûr, à Linde qui sera en mesure de proposer des produits toujours plus en adéquation avec les attentes des clients.
L’automatisation des chariots, devant évoluer vers l’autonomie grâce à l’intelligence artificielle, constitue une priorité pour le groupe allemand qui entend ainsi contribuer à pallier les problèmes de main-d’œuvre. En plus de lui permettre d’améliorer en continu ses produits, c’est également un moyen pour lui de lancer une nouvelle activité : la commercialisation de téléservices.
Christophe Duprez
Un nom propre devenu commun
Si elle existe depuis 150 ans, la société Fenwick est devenue Fenwick-Linde au milieu des années 1980, à la suite du rachat de sa branche manutention par l’industriel allemand Linde, lequel appartient depuis 2006 au groupe Kion, deuxième constructeur mondial de chariots industriels. L’attachement viscéral des Français à la marque Fenwick, dont le nom est aux engins de manutention ce que Frigidaire est aux réfrigérateurs, explique que ses chariots sont toujours vendus sous leur dénomination d’origine, alors qu’ils le sont sous la marque Linde partout ailleurs.
CD
Sandra Libarre (Am. 209).
3 questions à Sandra Libarre (Am. 209), responsable de l’amélioration continue au sein de Fenwick-Linde, filiale française du groupe Linde Material Handling
AMMag : Quel a été votre parcours professionnel depuis votre sortie des Arts ?
Sandra Libarre (Am. 209) : Mes différentes fonctions ont toutes un point commun : il s’agit à chaque fois d’une création de poste. Après mon diplôme obtenu en 2010, j’ai démarré ma carrière en Alsace, à Haguenau, comme responsable amélioration continue chez le fabricant de compteurs d’eau, de gaz et d’électricité Itron. J’ai ensuite intégré en 2016 Eurofins où je travaillais sur la partie environnement-laboratoires d’analyse d’amiante comme responsable du pôle Lean Manufacturing, Industrialisation et Maintenance. En parallèle, j’ai commencé à enseigner au Cesi de Strasbourg en 2015. En 2017, j’ai intégré SNR Cévennes, une entreprise spécialisée dans le roulement automobile, en tant que responsable de l’excellence opérationnelle et des services techniques. Enfin, j’ai rejoint Fenwick-Linde Operations en 2022 pour m’occuper de l’amélioration continue et de l’excellence opérationnelle des deux sites(1) français du groupe, situés près de Châtellerault [Vienne] et qui emploient plus de 700 personnes.
AMMag : En quoi consistent vos missions ?
S.L. : Membre du comité de direction, je dois tout d’abord faire prendre conscience aux différents manageurs que le changement peut s’opérer par des initiatives majeures qui ne nécessitent néanmoins pas de bouleverser tout le processus, et par d’autres, plus discrètes, d’accompagnement des collaborateurs. Leur adhésion me permet de pénétrer chaque département pour établir des feuilles de route dans une optique d’amélioration et de vision globale des projets prioritaires. Je dois ensuite mettre en place les processus d’excellence opérationnelle en identifiant les leviers d’amélioration sur l’ensemble de la chaîne de valeur : R&D, production, chaîne d’approvisionnement, SAV… Cela passe par la formation, pour laquelle nous avons la chance de bénéficier d’une école interne. Enfin, je suis chargée de l’efficacité de la gestion des coûts et de la productivité via le suivi des indicateurs du site, et de la mise en place des plans d’action qui en découlent. La finalité du Lean n’est pas de supprimer des postes, mais de les conserver en les réorganisant pour que les opérateurs y gagnent en qualité de vie et en sens à leur travail, et l’usine en productivité.
AMMag : En quoi votre formation aux Arts vous est-elle précieuse ?
S.L. : Je suis issue de la formation par l’apprentissage : j’ai suivi un cursus d’ingénieure en génie industriel de 2006 à 2009 à l’Ensam de Paris, en partenariat avec le CFA Ingénieurs 2000, en alternant cours et périodes en entreprise, dans le monde industriel. J’ai eu la chance d’intégrer MBDA où j’ai travaillé sur le projet de cœur artificiel Carmat, sur la CAO des outillages nécessaires. J’ai ainsi bénéficié d’une formation très complète qui m’a permis de mettre en application immédiatement ce que les Arts, grâce à la grande variété de cours qu’ils proposent, m’enseignaient en parallèle de façon théorique. Ma promotion regroupait des profils très variés, aux projets tutorés d’apprentissage très différents, et avec lesquels il était passionnant d’échanger lors des TP et TD. Grâce à cette formation, je suis capable aujourd’hui d’intervenir sur un périmètre très large. Un vrai plus ! J’ai même eu la formidable opportunité, après cela, de poursuivre mes études une quatrième année, toujours à l’Ensam de Paris, en mastère spécialisé Lean production et logistique. Je suis donc sortie de l’école avec, en poche, à la fois un diplôme d’ingénieur, une spécialité – le Lean – et une expérience de sept ans dans le monde du travail. Ce qui m’a permis d’accéder très rapidement à des postes de direction, dès la fin de ma période d’essai chez Itron.
CD
(1) Pour mémoire, l’usine Fenwick française a été spécialisée dans l’assemblage de transpalettes alors qu’autrefois elle fabriquait aussi des chariots de différentes catégories. Le reste de la production a été transféré dans l’usine italienne de Luzzara, qui est spécialisée dans la production d'une série de gerbeurs de 1 à 1,6 t ou encore dans celle des préparateurs de commande au sol de 2 à 2,5 t.
Toutes les photos : © Linde (sauf Sandra Libarre : DR)