Des treillis pour l’industrie
On n’assiste pas tous les jours à la naissance d’un nouveau procédé de fabrication industriel, qui plus est dans l’Hexagone ! Créée en 2023, la start-up Tetmet, spécialisée dans la fabrication de treillis 3D en acier, aux multiples avantages environnementaux, vise à mettre en œuvre une première ligne de production d’ici 2027. Elle vient d’obtenir ce 2 avril à Paris, dans les locaux de l’Automobile Club de France, le Grand Prix ACF Autotech 2025.
____________________
Par Christophe Duprez
Publié le 2025-04-07
Treillis en cours de réalisation par un robot 6 axes. © Tetmet pour toutes les photos
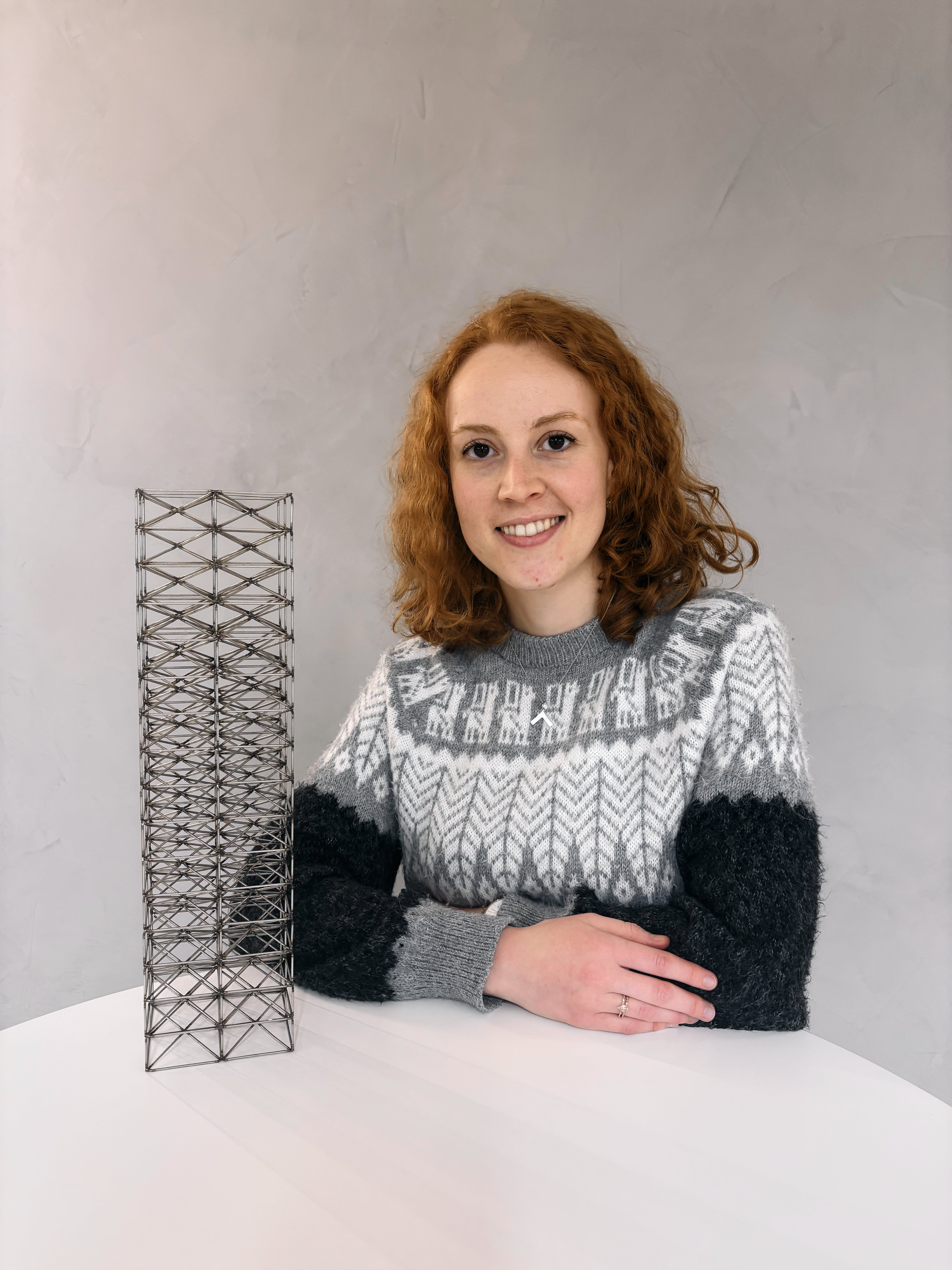
Le projet est né il y a 15 ans dans un laboratoire aux Pays-Bas. Dans le cadre de ses recherches, le fondateur-directeur général de la start-up Tetmet, Tom Vroemen, ingénieur en mécanique passé par l’Executive MBA de HEC Paris, s’intéresse au treillis.
Pour l’expliquer,
Rachel Azulay (Ai.217), responsable de l’ingénierie d’application chez Tetmet, prend l’image de la tour Eiffel : « L’ensemble est particulièrement résistant alors qu’il est constitué de poutres, sans qu’il y ait besoin d'avoir de la matière partout. Le treillis, qui appartient à la famille des matériaux architecturés, reprend ce principe-là… mais de manière miniaturisée ! »
Si les matériaux architecturés sont connus depuis quelques années déjà, ce procédé sophistiqué d’assemblage de tiges métalliques, qui associe microsoudage et découpe laser, est en revanche totalement nouveau.
L'avantage majeur du procédé baptisé Adaptive Space Lattice Manufacturing (ASLM) réside dans la réduction de masse : la matière est placée exclusivement où elle est nécessaire. De plus, ces arrangements de poutres peuvent posséder des propriétés mécaniques encore plus intéressantes. Ils peuvent être utilisés pour de la dissipation d’énergie, du filtrage, des renforts, voire même des agencements qui empêcheraient des changements de dimensions dus à la dilatation thermique. Le fait qu’ils soient creux autorise de surcroît le passage de câbles et l'air qui circule s’avère précieux pour certaines applications. Enfin, cette solution est aussi frugale que circulaire grâce un procédé de production économe en énergie et au recours à une seule matière, en l’occurrence l’acier, recyclable de surcroît.
Or, en 2010, il est encore trop tôt pour penser l’appliquer à l’industrie : Tom Vroemen imagine en effet une solution à base d’intelligence artificielle dotée d’algorithmes programmés pour l’apprentissage automatique (machine learning) et de robotique – des technologies alors insuffisamment mûres… Ce qui n’est plus le cas en 2023 où il collabore étroitement avec un spécialiste du premier et où la seconde s’avère beaucoup plus accessible financièrement… Qui plus est, le marché est demandeur de structures allégées, économes à la fois en énergie et matériaux ! Tetmet voit le jour.
Treillis militant
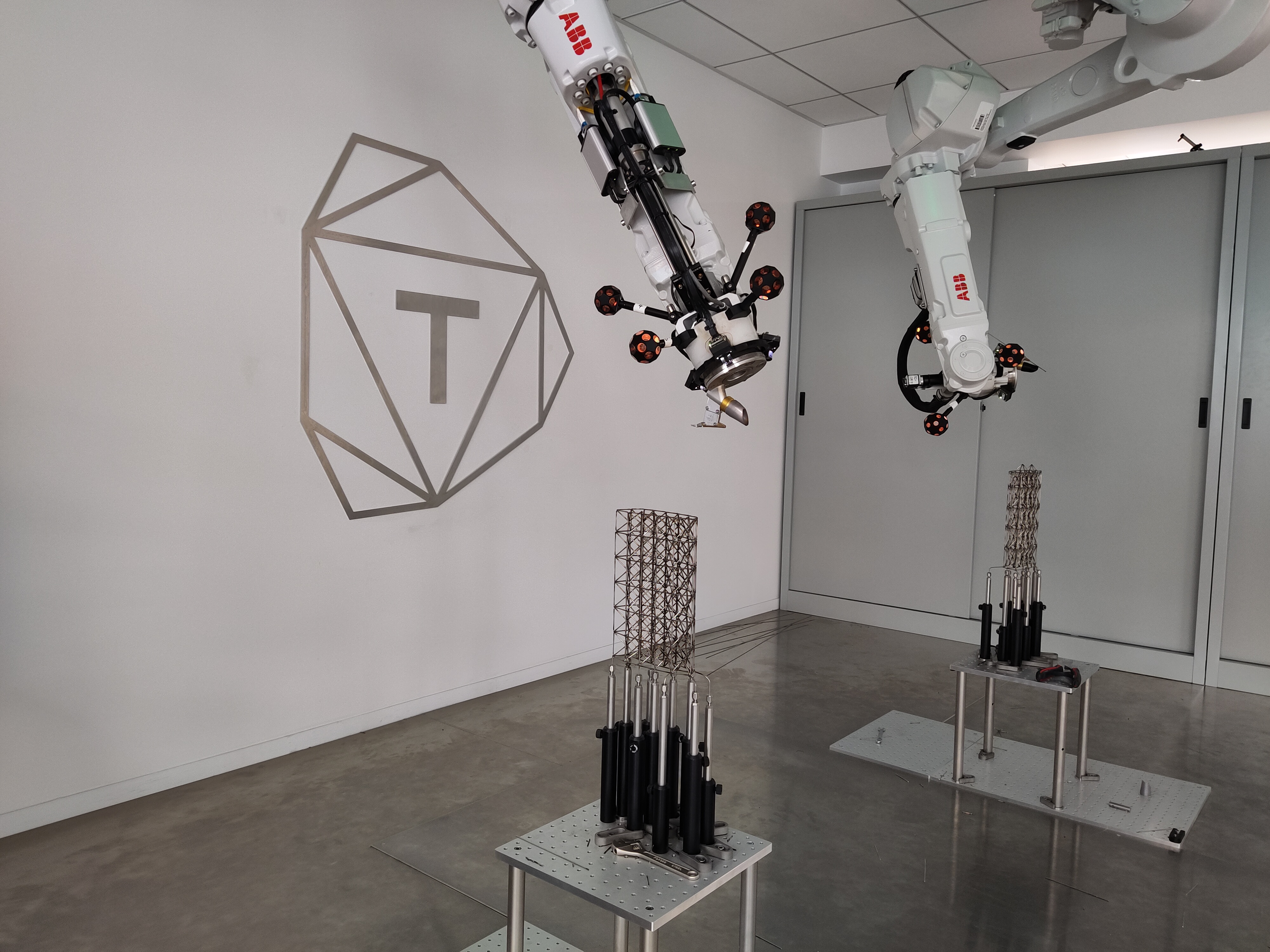
Pour élaborer son treillis, la start-up, forte aujourd’hui d’une douzaine de collaborateurs, utilise un robot 6 axes standard du marché qu’elle démonte en partie pour l’adapter. Il se retrouve ainsi augmenté à la fois d’un système de distribution de fil – pour le moment exclusivement en acier, économique et abondant, mais à terme dans d’autres matériaux qui enrichiront le catalogue – et d’un laser en fibre optique. Ce dernier découpe la bobine de fil métallique, le matériau de base de la structure à fabriquer, en petites tiges qu’il assemble ensuite en les soudant, au fur et à mesure, de manière à obtenir une pièce.
Si le robot ne nécessite qu’une simple prise électrique pour fonctionner, le soudage est réalisé sous atmosphère protectrice car on a recours à du gaz argon. Celui-ci est distribué à la jonction du rayon laser et de l’extrémité du fil, dans le but d’ôter l’oxygène en ce point précis afin d’éviter toute oxydation de la soudure.
En matière de logiciel, Tetmet a développé un programme pour concevoir des treillis optimisés, et un autre pour contrôler les robots. L’outil de conception est un « plug-in » – en bon français un module d’extension – conçu pour se greffer à des logiciels existants via une interface qui leur apporte de nouvelles fonctionnalités. « L’équipe de l’ingénierie d'applications, que je dirige, met au point un premier design, amélioré au fur et à mesure de nos simulations et de l’apport de connaissances, concernant les endroits critiques et l’orientation des barres notamment. À terme, l’enjeu consistera à enrichir notre logiciel de design (ndlr : de conception) de solutions d'optimisation capables d’aider ses utilisateurs à concevoir eux-mêmes des pièces, sans notre assistance », explique Rachel Azulay.
Voir la vidéo ici.
Les prochains défis à relever
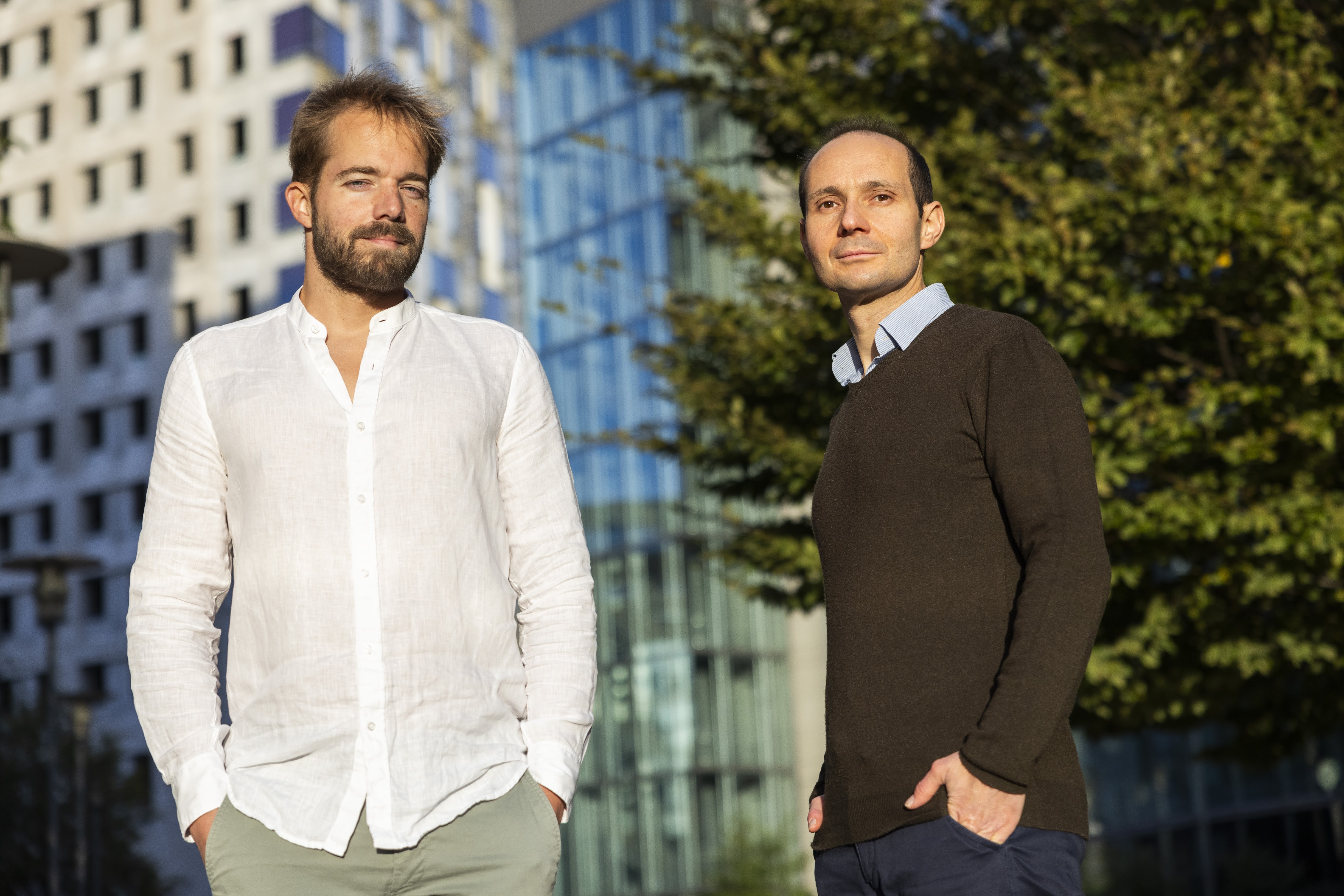
Avant de pouvoir opérer le passage à l’industrie (voir encadré), Tetmet doit en effet parvenir à relever trois grands défis.
La start-up travaille depuis son laboratoire de la Grande Arche (à La Défense) aux deux premiers, étroitement liés : la qualité et l’automatisation. « Pour le moment, c’est le contrôle visuel des soudures qui nous donne les indications sur la qualité », explique
Nicolas Chaignet, directeur commercial de Tetmet (à droite, au côté de Tom Vroemen). L’équipe s’applique ensuite à modifier une multitude de petits paramètres – le serre-fil, les ressorts, la distribution de gaz, l’énergie du laser… – pour corriger les imperfections. Or, le but est d’automatiser progressivement cela.
Actuellement, un opérateur lance chaque étape de production après avoir validé visuellement les éléments nécessaires à la parfaite exécution d'une tâche. Certaines de ces démarches s’avèrent particulièrement complexes comme l’évaluation de la distance, du positionnement des tiges ou encore de la qualité de la soudure. L’objectif est de ne lui laisser que la supervision générale du procédé. Ce qui s’avère possible grâce aux progrès de l’apprentissage automatique supervisé, de plus en plus capable de déceler les erreurs et les paramètres à modifier.
À ce jour, le procédé de fabrication des treillis n’est pas totalement automatisé et nécessite encore partiellement une réflexion, une intervention et un contrôle humains. L’objectif consistera donc à réduire progressivement cet apport pour parvenir à une solution entièrement gérée par la machine.
En revanche, le troisième défi, la rapidité d’exécution, ne pourra être relevé que directement sur les sites de production. Dans son laboratoire, la start-up est en effet bridée par l’absence d’équipements de protection sur ses robots qui l’empêche de les faire fonctionner à une vitesse élevée. Chez ses partenaires, elle pourra optimiser le procédé sans limitation, voire associer, en fonction des pièces à élaborer, plusieurs robots qui collaboreront. « C’est ainsi que nous parviendrons à remplir les objectifs, notamment de l'automobile, demandeuse de cadences rapides », précise Nicolas Chaignet.
Des collaborations avec les grands secteurs industriels
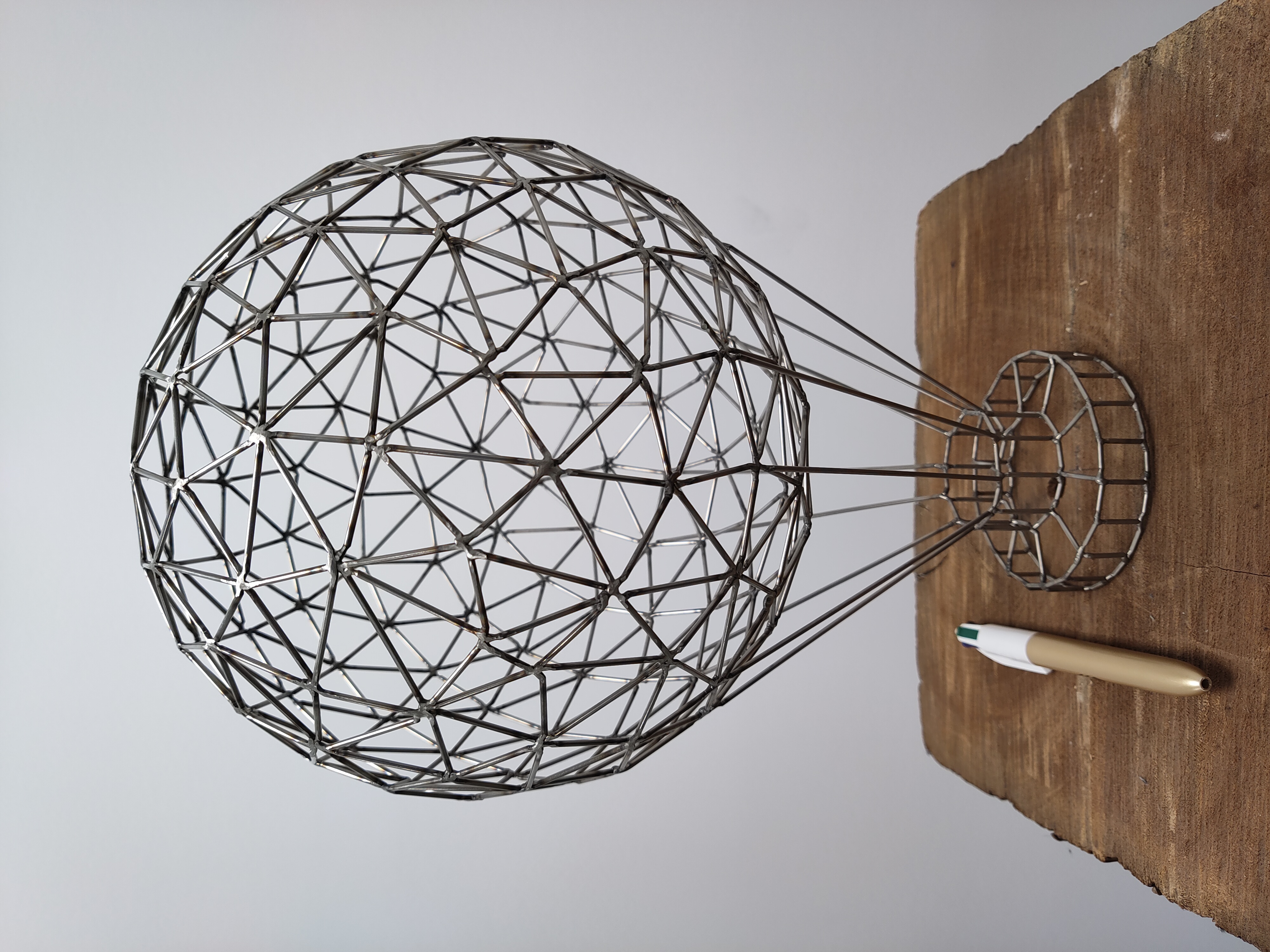
Si Tetmet ne peut, pour des raisons de confidentialité, dévoiler l’identité des principaux acteurs avec lesquels elle collabore, Nicolas Chaignet confesse travailler en majorité avec le secteur de l’automobile, voire avec de grands constructeurs européens.
Ce constat s’explique par la pression qu’exerce l’arrivée massive de la concurrence chinoise sur le marché. Ils forcent les fabricants occidentaux à se montrer plus performants.
Ces fabricants doivent également se réinventer, en allégeant notamment leurs véhicules pour des problématiques d'homologation : si certaines voitures n'atteignent pas un certain poids, elles n’intégreront pas la catégorie visée, avec des conséquences sur le régime fiscal.
L’enjeu de la perte de masse alliée à la résistance explique aussi des collaborations privilégiées dans les secteurs de l'aérospatial (lanceurs et satellites en particulier), la défense, le ferroviaire ou encore les machines industrielles, dont les fabricants cherchent à alléger leurs produits pour les rendre moins énergivores.
Christophe Duprez
En route vers l’industrialisation
L’objectif de la start-up ne consiste pas à produire en série dans une usine estampillée Tetmet, mais à équiper les robots des lignes de production des clients de son logiciel, le modèle économique s’appuyant sur la vente de licences.
Dans ses locaux de la Grande Arche, elle se limite à reproduire en treillis des pièces existantes soumises par les industriels qui souhaitent les alléger, en attendant d’en concevoir d’originales, impossibles à réaliser en dehors de sa technologie ASLM.
Ce site constitue donc essentiellement un laboratoire dédié à la recherche et aux preuves de concept, même s’il lui arrive occasionnellement, pour des clients dans l’aérospatiale notamment, de produire une pièce unique ou en très petite série.
Les choses devraient rapidement s’accélérer avec une première ligne de production automobile équipée au plus tard en 2027.
Lauréat du Grand Prix ACF Autotech 2025
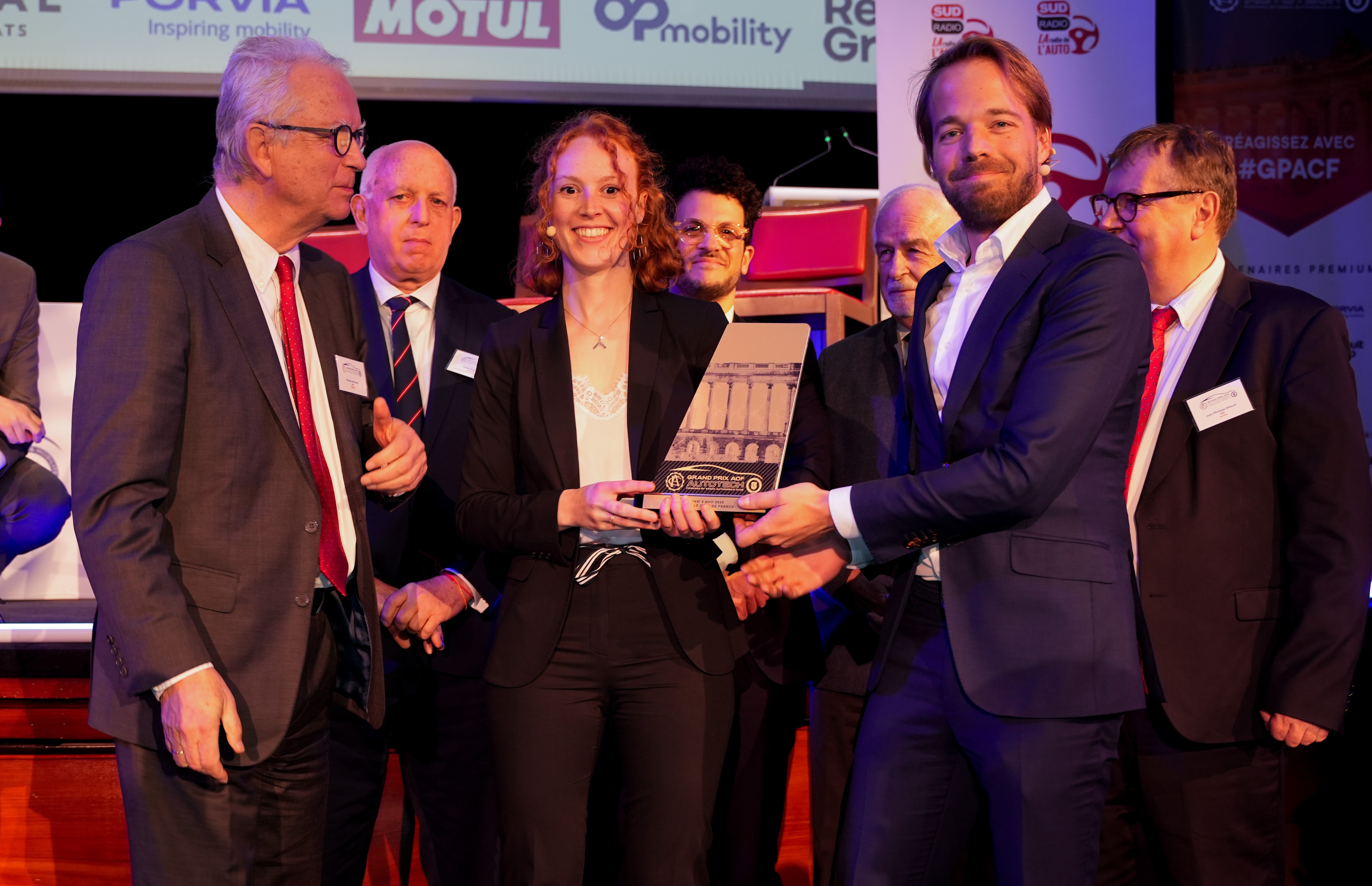
Ils n’étaient plus que trois à pouvoir prétendre emporter, le 2 avril à Paris dans les locaux de l’Automobile Club de France, au Grand Prix ACF Autotech 2025. Ce prix international récompense depuis 2017 les startups les plus innovantes du secteur automobile de la planète. « Nous avons postulé sur les conseils de différents contacts, parmi lesquels plusieurs de nos clients et le pôle de compétitivité européen de la mobilité Nextmove, auquel nous adhérons », précise Nicolas Chaignet. Lesquels ont eu le nez creux puisque Tetmet l’a emporté, obtenant tant les suffrages du public que ceux du jury constitué de grands noms de cette industrie.
C. D.
© Quentin Vaquez