Arquus s’adapte aux commandes cycliques des clients
Comment la société Arquus, ex-Renault Trucks Defense, filiale d’AB Volvo spécialisée dans la conception et la fabrication de véhicules terrestres blindés à roues, organise-t-elle sa production… qui dépend de charges variables et d’engins sur mesure ? Un vrai casse-tête pour un responsable de production.
____________________
Par Djamel Khamès
Publié le 2023-10-04
Objectivement, le contexte national et international s’est durci pour les industriels de l’armement terrestre français. De nouveaux concurrents, turcs ou sud-coréens par exemple, proposent des produits au rapport qualité/prix compétitif. En parallèle, le gouvernement français a étalé ses prises de commandes par une loi rectificative. Dans ces conditions, difficile d’entrer dans une économie de guerre prônée par le chef de l’État pour « produire plus, plus vite et moins cher ». La réponse à ce nouvel environnement concurrentiel passe notamment par le renforcement de l’innovation. Selon Emmanuel Levacher, président d’Arquus, « il y a la R&D financée en fonds propres, environ 20 millions d’euros par an, soit de 3 à 3,5 % du budget global, et il y a la R&D financée par les clients, forcément centrée sur leurs produits ». L’innovation peut aider les exportations à croître, l’objectif étant d’atteindre peu ou prou 50 % du chiffre d’affaires. Le Sherpa, véhicule créé exclusivement pour l’export, ou les tourelleaux(1) téléopérés Hornet sont typiques de cette démarche. La réponse aux commandes cycliques gouvernementales, quant à elle, passe principalement par l’adaptabilité de l’outil industriel. Arquus – dont les volumes annuels traités peuvent varier de 1 à 2,5 (69 259 heures d’activité en 2022, contre 175 000 en 2019) – a pris le taureau par les cornes, il y a trois ans environ, en lançant une vaste réorganisation de ses usines. Ce chantier, doté de 15 millions d’euros, a permis de les spécialiser. L’objectif est d’atteindre l’excellence en concentrant les compétences plutôt que de les laisser se diluer de-ci de-là. Depuis, le site de Saint-Nazaire (Loire-Atlantique) a été spécialisé dans la réparation ou la régénération des véhicules, l’usine de Marolles-en-Hurepoix (Essonne) dans la production d’organes mécaniques et de tourelleaux téléopérés, et celle de Garchizy (Nièvre) dans les caisses de blindés et la logistique de pièces de rechange. Enfin, Limoges (Haute-Vienne) s’est vu attribuer l’assemblage des véhicules neufs.
Limoges sous le signe du lean
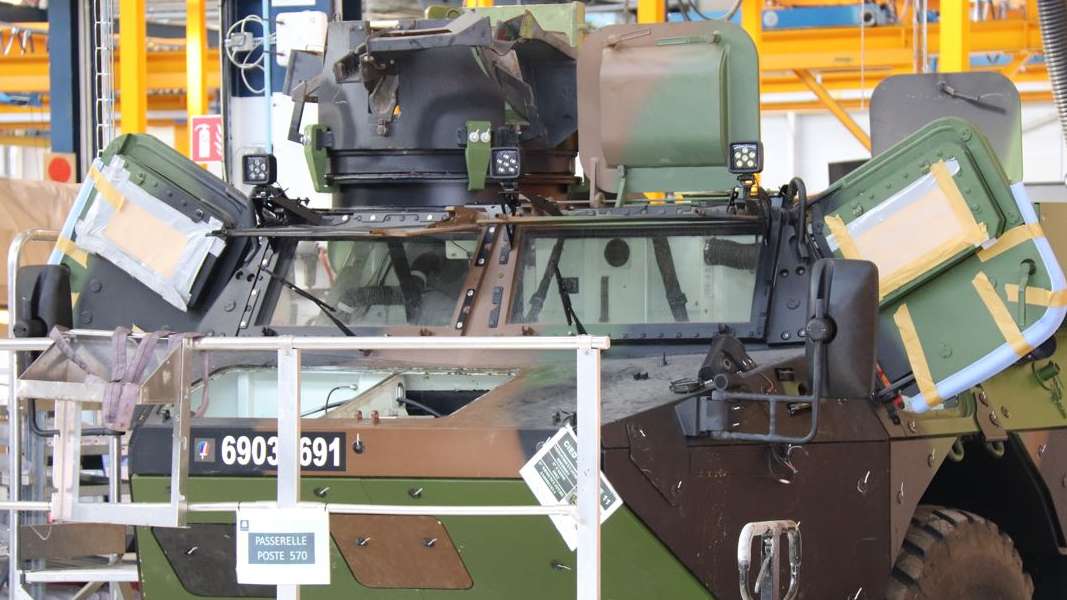
Parallèlement au soin apporté à l’éclairage de l’usine (privilégiant la lumière naturelle) et à l’amélioration des postes de travail, plus ergonomiques, le site de Limoges (15 000 m²) a bénéficié de nouveaux bureaux (qui ont permis de libérer de l’espace au centre de l’atelier), d’une troisième ligne d’assemblage et d’une cabine de peinture (tâche autrefois sous-traitée). Cerise sur le gâteau, des navettes, chargées de pièces depuis la nouvelle plateforme logistique (9 000 m²), alimentent en toute autonomie chaque poste de travail. Cette organisation est rendue possible par l’interconnexion du logiciel de gestion des stocks (WMS) et des ordres de fabrication, produits par le progiciel de gestion intégré (ERP). Ce nouveau mode de fonctionnement a libéré les opérateurs des incessants va-et-vient entre leur poste et les rangements où étaient stockés les éléments à assembler. L’avantage est double : moins d’erreurs dans le choix des pièces et charge mentale moins sollicitée pour une tâche, au final, à faible valeur ajoutée. Outre cette modernisation, Sophie Rol, directrice de l’usine Arquus de Limoges, met l’accent sur le nouveau triptyque « sécurité des salariés, qualité des produits et tenue des délais », conforté par la mise en place d’une démarche de lean management. La philosophie globale de cette méthode met l’opérateur au cœur de la production avec une adaptation de son environnement, de ses outils (zone kaizen) et des processus. Concrètement, de petites équipes autonomes, de 6 à 12 personnes, ont été créées. Selon la directrice, « cela a permis de résoudre plus rapidement les problèmes quand ils survenaient et, mieux, d’associer activement les salariés à l’amélioration continue du fonctionnement de l’usine ». Cette démarche lean est impulsée par 14 chefs d’équipe, 4 manageurs de production et 4 manageurs de logistique. Tous ont bénéficié d’une formation diplômante, d’une durée pouvant atteindre un an, en partenariat avec l’organisme de formation d’Arquus, l’Agence de formation, d’études et d’innovation (AFEI).
Le vrai défi industriel : l’adaptabilité
Le principal défi d’Arquus consiste à épouser en toute flexibilité les « stop-and-go » des commandes. « Les clients demandent de plus en plus de réactivité pour de faibles volumes, indique Sophie Rol. Malgré ces circonstances, nous devons rester performants. Les stocks de tôle, par exemple, en sont une belle illustration : comment livrer des véhicules dans six mois quand l’approvisionnement de ce matériau se négocie dix-huit mois plus tôt. Pour ne pas perdre de marchés, nous prenons notre part de risque en anticipant nos futures productions. » En tout cas, beaucoup a été fait – en matière d’organisation comme de formation – pour augmenter la probabilité de remporter le plus d’appels d’offres possible.
(1) Un tourelleau téléopéré est une tourelle équipée, placée au-dessus du véhicule blindé. Ce système permet de commander une arme sous blindage depuis l’intérieur du véhicule. L’opérateur, qui n’est plus exposé à l’extérieur, est ainsi protégé.